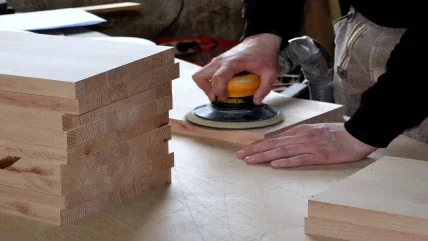
Summary
• Demand improved in the second half.
• Specialists joiners are doing better than volume manufacturers.
• Margins have been reduced.
• Joiners are not expecting growth this year.
The summer and autumn provided a welcome – and, to some, surprising – upturn in demand for joinery and the consensus in the sector is that the fourth quarter of 2009 did not see the dramatic tailing off experienced at the same time a year before.
There are also companies which say that, thanks either to specific sales strategies or their particular production niche, they actually had a good 12 months.
That said, however, the joinery industry consensus is that overall market conditions are still tough and that real sector-wide recovery is set to be a long, arduous process.
Small, specialist joiners are perhaps doing better than the volume manufacturers and their architectural counterparts but across the market there are still reports of companies taking on work well below value to keep going.
The seriousness of the situation is illustrated by the number of members the British Woodworking Federation (BWF) has lost to administration – 4% from January to the end of October, compared with 2% in 2006/07.
“The volume manufacturers are finding it harder than anybody else but everyone, without exception, is saying you have to run twice as hard just to stay still,” said BWF chief executive Richard Lambert.
“The general sense is that there is work out there, but you have to go out and look for it, you can’t sit and wait for it to come to you.”
RMI bolsters sector
Market areas said to be doing best are non-housing work in the public sector and repair, maintenance and improvement (RMI).
“There are still people with money and they are prepared to spend it on [improving] their homes,” said Mr Lambert.
According to one manufacturer, this had also helped the DIY market remain a joinery bright spot. “There’s been no real decline, with the [multiples] holding up well,” TTJ was told.
Mr Lambert, however, said that while RMI also provided business for small, specialist joineries, the work may be specials, which are more time-consuming and, although of a higher value, not necessarily higher margin.
Customers are also taking advantage of the situation, with some wanting work done at prices quoted six or nine months ago, or generally pushing for lower prices. “We’re having to cut prices because everybody is clawing for the same work,” said an architectural joiner. “Profit margins have fallen, partly because people want a bargain and, because there’s not a lot of work in front, you tend to take longer to do it.”
Another contact confirmed the BWF’s findings that there was slight improvement in the last quarter of 2009, a trend he attributed to some movement in the housing market, but principally RMI demand.
“Demand for joinery products is still determined, in the main, by the consumer [and current levels of confidence mean that] it’s refurbishment that really stimulates demand more than new build,” he said.
The “improve not move” trend, he said, was certainly having an impact on demand for higher specification timber windows, as was the drive for greater energy efficiency in the home. But in the volume windows market it was a different story.
“There are suicidal prices going on from the volume manufacturers and that’s always distressing to see. I can’t imagine a lot of bottom line profits being created at the moment.”
Staircase manufacture has been particularly badly affected by the slump in new build, according to one producer. The company did, however, report some pick-up in activity in the fourth quarter. Sales were still down year on year, but the business was also now getting something of a boost from the return to building houses after the apartment sector reached saturation point.
Meanwhile, merchant joinery demand is still reported to be generally depressed, although there seems to have been some movement towards the end of the year.
Joiners also say they are continuing to be hit by slow payment from contractors. “People are coming up with any excuse not to pay,” said the architectural joiner. “We’ve been dealing with the same companies in the good times and now we’re struggling to get money out of them.”
His company, he added, had struggled for the past three or four months and with thin order books for January, was having to lose some staff, having already cut its workforce by 40% in 2009.
Diversity spells success
One of those companies reporting a better performance in 2009 supplies a “diverse range of joinery products”.
“The only downside is that our margins aren’t what they should be, but we’re still making a decent profit,” said a spokesperson. “And we would never contemplate selling things at cost.”
He also acknowledged that 2009 had been hard work, but said that overall sales were up and his order books had been “healthier than ever”.
“Our worst month was May, when it seemed to drop off the planet, but since then it’s been building and building to the point we’re now snowed under; we just can’t make it fast enough.”
Timber windows, in particular, were “flying” and fire doors and entrance doors were also in demand. His view was also that the merchant sector was now improving, benefiting from the number of people made redundant from building firms, setting up in their own right to take on smaller jobs.
In December, the company was still happy with the orders it had to February, however it was also more cautious for the rest of the year.
“I’m happy but with one eye on next month; you never know what’s around the corner. It just takes the banks to do something daft and everybody loses confidence,” said the spokesperson.
2010 uncertainty
Other contacts were not expecting any significant growth this year:
“We‘re pitching for a flat 12 months; anything above that is going to be a bonus,” said a volume manufacturer.
There’s a similar feeling in the architectural sector. “The building trade was the last one to go into the recession and I guess it will be the last one to go out. People’s confidence is not there,” TTJ was told.
Mr Lambert thought the market may start to pick up later this year but, with little liquidity in housing and the pending general election creating uncertainty, 2010 would not be any easier for the joinery sector.
“Construction will lag behind the overall economy and joinery is always at the end of construction so I think we’re in for a difficult year. In fact, I don’t think we’ll see any improvement until early 2011, and that’s assuming everything goes well,” he said.
But, although chancellor Alastair Darling’s pre-budget report in December included hefty public spending cuts, Mr Lambert was hopeful that the impact of this would be delayed.
“They’re talking about reining public spending back after the election, but a lot of money is already committed so, with a bit of luck, we won’t see the usual tailing off we get [in the run-up to elections] ,” he said.
But further highlighting the diversity of experience across the market, another contact was optimistic about prospects beyond the first quarter, although acknowledged it would be hard work .
“Joinery is still a fantastic industry to be in,” he said. “But it’s up to us to extract more profit opportunities by developing products for the future. Integration of building products is important and supplying factory-made buildings has to be encouraged and developed.”