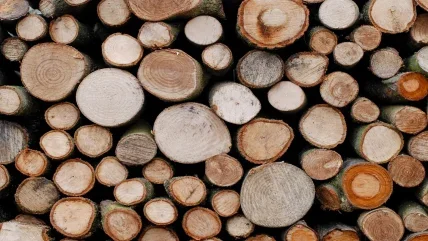
Summary
• Timber frame has 23.4% of UK new build housing – 30,656 units in 2011.
• Social housing funding cutbacks are biting deeper.
• Self-build is now the UK’s biggest ‘builder’ and a strong timber frame market.
• Industry innovation focuses on energy-saving and build efficiency.
One word recurs in conversation with timber frame companies on the state of the market – pressure. The pervading view is that there are too many people after too little business and it’s making 2012 at least as challenging as 2011. That said, the sector is not entirely without its brighter spots, with retail, self-build and more specialist sectors, notably eco-homes, offering some relief.
At the heart of the matter currently is the fact that, despite some better news, such as improved profitability at Barratts and Persimmon, the housing market is still not firing up significantly. In fact, the public housing sector is deteriorating as government cuts bite.
“We’re at a lower level as an industry than six months ago,” said Kingspan Potton commercial and sales director Tony Hutchison. “We made a reasonable profit in 2011, but the order book got smaller. We’re now in our seasonally slow period, but also seeing funding for affordable housing gradually reducing. Government may have a ‘get Britain building’ strategy through to 2015, but right now housing associations don’t have the funds they need.”
Stewart Milne Timber Systems group managing director Alex Goodfellow also said there were “signs of slippage, with [social housing] projects put on hold”, while Pinewood Structures managing director Geoff Arnold said public funding uncertainties led to a “shortfall of work for the industry in the first quarter”.
“It’s no surprise government changes in social housing funding and planning, giving more authority to local government and making the process more complex, would add to the industry’s woes and that it would take time to figure a way out of the mess,” he said.
Further evidence of the competitiveness of the market has been a recent discussion among timber frame manufacturers on the LinkedIn business networking site. Under the heading “is the timber frame market over-saturated?” Eco Frame Systems managing director Steve Gambrell said industry capacity had not sufficiently contracted in line with demand. In fact more entrants had come from timber companies which had closed or made redundancies. As a result, bids for projects were being made at “35% below realistic”.
“Cutting prices to levels that don’t cover costs to secure business is devaluing the market,” he said. “It’s unsustainable.”
Recently the private housing market does seem to have given slightly more cause for optimism. Mr Arnold said latest results in the sector had boosted confidence and agreed with others that business in the south-east, was doing “relatively well”. Talk at a recent UKTFA conference was also of “wheels slowly turning”, even “green shoots”. However, the rider to this is developers continuing to depress prices.
“As they’re discounting their prices so much, developers are reverting to using surveyors to invite bids from six to eight companies on the basis of absolute best value,” said Mr Hutchison
Mr Arnold also said project orders were placed last minute, “adding to the pressure”.
Self-build dominates
But there seem to be fewer provisos about post-crunch recovery in self-build, a traditional bulwark for timber frame.
“Self-build is now the largest ‘builder’ in the UK,” said UKTFA chief executive Andrew Carpenter. “Government emphasis is helping maintain its popularity and some self-build specialists reported record years in 2011.”
At Kingspan Potton self-build business is 50% of sales and grew 10-15% last year.
“Given market competitiveness and improved land availability, if people have the money, it’s a good time to build,” said Mr Hutchison. “An added benefit is that self-builders are more concerned with quality and value – our average self-build package is now £70,000.”
Underlining confidence in the sector, Kingspan Potton has just built a fourth home on its St Neots self-build show site and Wyckham Blackwell this week announced the launch of WB Timber Innovations to service self-build.
The market bright spot highlighted by Eco Frame Systems is its business supplying houses to the international Passivhaus energy performance standard.
“This may still be a relatively small market, but the term Passivhaus is gaining brand awareness, and we believe our focus here will pay dividends,” said Mr Gambrell.
Kingspan Potton, which is supplying SIPs-based homes to Barratts’ zero carbon Hanham Hall development, also believes the eco-home market bodes increasingly well for timber frame.
“Timber not only has the inherent advantage of renewability, it also lends itself to more sophisticated ways of cost and energy-efficient offsite prefabrication,” said Mr Hutchison.
Retail construction
Timber building’s environmental hook has given it impetus in retail too.
Mr Arnold said that two of Pinewood’s highlights last year were supplying wall systems for Tesco stores in Barnstaple and Dawlish. The retail giant, which was the leading the way in eco-store building, had “retrenched” on its build programme following its poor results but timber framers are generally optimistic about their retail prospects longer term.
“We’d rather it happened sooner rather than later, but eco-stores are clearly the way the sector will go,” said Mr Arnold.
Mr Hutchison agreed. “Most big retailers now have an eco-store strategy and almost by definition that means glulam or timber frame. While it’s not an area we’re currently in, we may put it on the shopping list,” he said.
Stewart Milne also reports timber frame holding its own in commercial sectors, notably hotel and student accommodation markets where “speed of build is crucial to get quick return on investment”. Highlighting the kind of project timber frame can deliver Mr Goodfellow pointed to the £40m student village at Bradford University that Stewart Milne has just completed. It was not only delivered to a “stringent deadline”, but also tough environmental criteria. “It’s the first building of its kind to achieve BREEAM excellence,” he said.
As evidence of the UKTFA’s contention that the timber frame sector has also responded to tough times by becoming “more agile” and adopting competitiveness-boosting new approaches and technologies, Mr Carpenter highlighted the focus of its Timber Frame Industry Think Tank on the use of Building Information Modelling. “Innovation is a key theme for us in 2012,” he said. “Interesting new products and services are also coming out of our fire testing work and we’re organising an innovation day at the Swindon BuildStore.”
Underlining its commitment to pushing back technical barriers, Stewart Milne highlights the roll-out of its Code for Sustainable Homes level 4 Sigma II ultra energy-efficient prefabricated closed panel system, which promises a finished structure 30% faster than conventional build.
Kingspan Potton, meanwhile, has been selling the energy and quick build benefits of its SIPs to other construction system providers, notably as infill panels for steel frame.
Little respite in 2012
Looking at the rest of 2012, timber frame suppliers expect little overall respite in market conditions. Indeed, Mr Carpenter said consolidation across the “construction community” would not be a surprise. But medium to longer-term confidence remains that growing awareness of timber frame’s time and cost-saving potential, combined with its established environmental merits, can help it increase UK market share beyond its current estimated 23.4%.
“The government has set targets to achieve zero carbon homes by 2016 and in a cost-effective market manner,” said Mr Goodfellow. “Timber frame has a large part to play in this step change.”
Mr Arnold said the industry and its organisations have to do more to “engage with developers” to make timber frame the “de facto way of housebuilding” and also may struggle to rebuild design capacity when an upturn comes. But he was also cautiously optimistic. “In particular, I believe private developers who decided it was more cost-effective [in the downturn] to build slower in masonry, will return to timber frame due to its thermal performance and the need to build faster.”
Further expressions of faith have come from Persimmon, which has just expanded its Space4 timber frame plant, and Accord, a housing association group which last year opened a new 200-unit annual capacity factory and is now considering a second. The latter’s main objective is to supply its own developments, but it is receiving third-party enquiries. Head of project development John Bedford acknowledged this might be seen as “unfair competition” given Accord’s access to public funding.
“But if we’re delivering quality, affordable, good-looking housing that residents like, it will help the development of the market,” he said.